Industrial Displays
From Analog to Industry 4.0
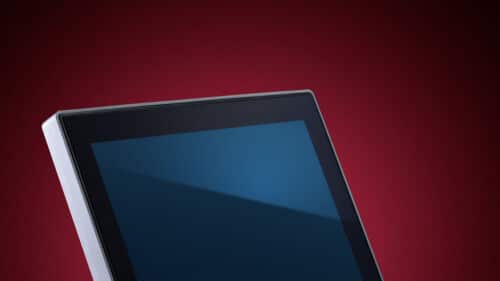
Industrial display vs. commercial displays
Industrial displays and commercial displays serve different environments and often have very different requirements when it comes to durability. Industrial displays are built for resilience and to handle extreme conditions such as dust, moisture, high and low temperatures, and vibrations. They are expected to function as required, and you often find them with rugged casing, with higher-grade components and strict quality control to ensure longevity. Other important differences that separates industrial from commercial displays are glove-friendly touch screens, high brightness for better visibility in sunlight, and broad signal compability to ensure that they meet different industrial application needs. Industrial displays are generally produced in smaller quantety and at the same time expected to be available for 5-10 years.
Commercial displays are designed for a far less demanding indoor environment and are more likely to be found in a retail space than on a construction site. Hence, they don’t need to meet the high demands of an industrial display. They typically have plastic casings and focus on aesthetics with high-resolution screens and user-friendly interfaces. While still durable, they’re not designed for the extended service life required in industrial contexts and offer fewer installation options.
Industrial displays also excel in operational performance with industrial-grade motherboards, wide viewing angles, and a variety of power input options. They can withstand severe temperature fluctuations and are customizable to specific operational requirements, including display quality and operating temperature ranges.
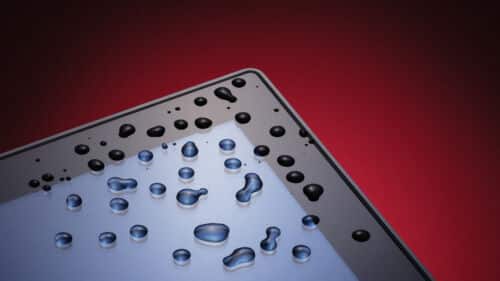
Applications and Usage
Industrial displays are essential in a multitude of industries. They are not just confined to embedded systems but extend their usage across a variety of fields and environments.
Embedded within heavy machinery and production lines, industrial displays act as control panels that allow detailed management of manufacturing processes. They’re the eyes and ears on the ground in sectors like oil and gas, pharmaceuticals, and manufacturing, where they monitor and visualize critical process data, enhancing quality control and operational efficiency.
Industrial displays are very common in outdoor applications, such as in the harsh environments of construction sites, marine explorations, and mining operations, where they must endure varying weather and temperatures. Here they can help their users with overlooking machine performance the surrounding environmental conditions, as well as a visualizing tool in data acquisition systems.
In transportation, displays are an essential component. They provide navigational and engine status information for vehicles across rail, air, and marine systems. They also serve a critical function in safety systems within high-risk environments like nuclear facilities and chemical plants, offering real-time alerts to avert potential hazards.
The medical field relies on the precision and dependability of industrial displays in devices for patient monitoring and diagnostic imaging, where clarity and reliability are indispensable.
In the energy sector, monitoring power generation and distribution, especially for renewable sources like wind and solar, is facilitated using industrial displays. And in the food and beverage industry, processing conditions and compliance with health and safety standards are ensured through displays.
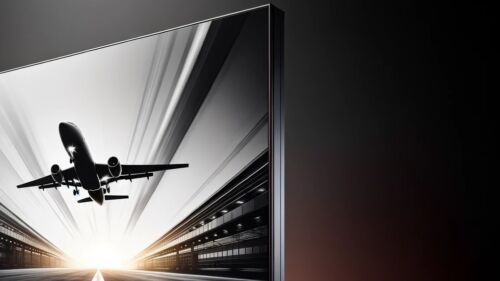
Technical Specifications and Types
LCD and IPS
Today, you can find almost as many variations of industrial displays as there are fields of application, all with their own unique selling point. Now that we have established that industrial displays are a vital part of many modern industrial applications and that they can be found in a variety of industries, let’s look at some of the different types of displays that are more commonly used.
• LCD Technology: The use of Liquid Crystal Display (LCD) technology in industrial settings is prevalent due to its energy efficiency, which can be crucial in reducing operational costs and meeting environmental standards. LCDs utilize a liquid crystal solution sandwiched between two polarizing filters and glass layers, with the crystals aligning to allow varying levels of light to pass through in response to an electric current. This energy-efficient operation is especially beneficial in industrial applications where displays may need to operate continuously.
• IPS Panels: In-Plane Switching (IPS) panels are incorporated into industrial displays for their wide viewing angles, which can reach up to 178 degrees horizontally and vertically, ensuring that display colors and images remain consistent, even when viewed from sharp angles. This is particularly important in industrial settings where operators may need to monitor displays from various positions. IPS technology also offers superior color fidelity and better color accuracy, which is crucial for tasks that require precise color differentiation.
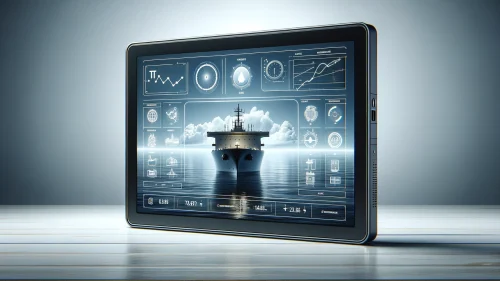
Technical Specifications and Types
Specialized Solutions and Future Directions
• Outdoor and High-Brightness Environments: For brightly lit or outdoor industrial environments, displays must overcome the challenge of direct sunlight or high ambient light conditions. LED displays are not only bright but can be designed with high-nit outputs, making them readable even in direct sunlight. Additionally, these displays can come with anti-reflective and anti-glare coatings, which reduce the impact of external light sources and improve visibility.
• Rugged: These industrial displays are engineered to withstand extreme temperatures, vibration, shock, and other challenging conditions. They are often built with rugged casings and are rated according to Ingress Protection (IP) codes, which indicate their level of resistance to dust and water, ensuring reliable performance in various industrial settings.
• Customized displays: Custom displays are increasingly becoming more common, providing customers with the exact features they need, such as tailor-made cover glass with unique specifications like special corner radii, varying thickness, hardness, and surface treatments, as well as drilled holes and screen-printed logos; additionally, touch sensors are customized to offer a larger active area in proportion to the external dimensions, ensuring their precise industrial needs are met with precision.
• Emerging Technologies: Looking ahead, emerging technologies such as Organic LED (OLED) and Quantum Dot LED (QLED) are on the horizon for industrial applications. These technologies promise even better color accuracy, contrast ratios, and energy efficiency. With the increasing focus on sustainability, industrial displays are being designed with power-saving features, such as automatic dimming and power-off timers, contributing to lower energy consumption and a reduced carbon footprint.