What is embedded testing?
Embedded Testing
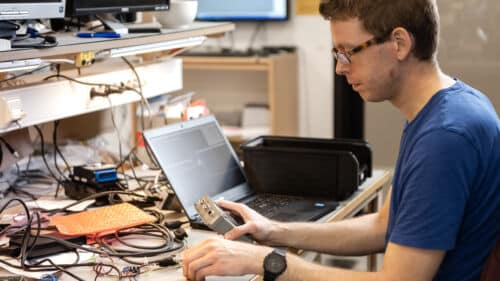
The Testing Process
In the development phase, the initial step is verification to ensure that the products delivered meet the customer’s expectations. Extensive testing and trials are performed on the first prototypes, and placements and soldering of components are inspected while voltages are measured to ensure that limits are not exceeded. Finally, the operating system is run to verify all interfaces, and the prototype is connected to the intended environment to check for success. If the verification is successful, the prototype is produced according to the specifications and functions as planned in the application.
One essential part of any test procedure, included embedded products, is testing during manufacturing. This process is generally referred to as production testing, or functional testing. In product testing, the design goes through a subset of the complete set of tests for validation or verification. The purpose of the production testing is to assure that a manufactured product is working according to this subset of tests.
It is important to remember that when a unique unit passes the production testing, it will assure that that unique unit is working as required. And when a unit passes validation and verification, it is assured that the unit’s design works properly. Two different, but equally important indicators of function and quality, and one cannot be substituted for the other.
Verification and validation
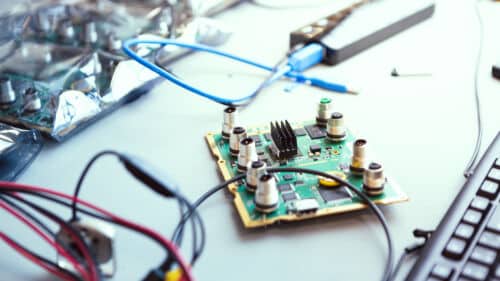
Embedded testing
Testing at Hectronic
At Hectronic, we have a tradition of developing our production test systems in-house. Over the years this has shown to give us several huge advantages, the main advantage being that knowledge transferred between testing and development becomes very efficient. Apart from that, it’s also cost efficient, and the system maintenance is easier. To have the production test system development in-house means that no external consultants are needed when service is required. And this is extremely important when servicing a system that is located in another part of the world at our production site in Taiwan.
The software suites for production test systems are all named “HecFCT”. HecFCT is an acronym that stands for “Hectronic Functional Control Testing”. The name has been around since Hectronic developed its first production test software.
In addition to the software suite, almost all customer unique systems have their own customed production test hardware. Even though each production test hardware is customized, they are all based on Hectronics building blocks for production test design and are running on a Hectronic computer module. This has shown to be more efficient than using of-the-shelf products to build a test system hardware, both in regards of maintenance and to elongate the lifespan of the hardware after installation.
Each test system has some customized code for each unique project, but the software base and test control code are the same for all test systems. This makes the development easier for the developers which in turn results in faster and more reliable deployment.
In-house development
Advantages with in-house testing
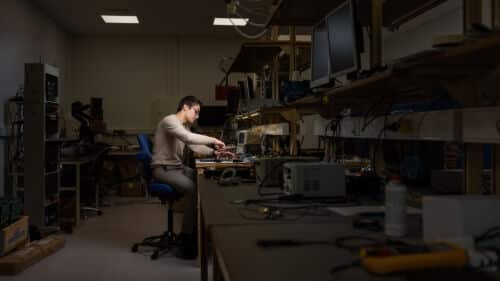
Test system code
HecFCT 2 - the next generation
Hectronics test system software suite has always been designed to perform functional and reliable tests of the end customers product. To ensure that we continue to perform the same quality tests, we decided to update our test system code. The project was recently finished the project and updated the code to the next generation software, now called HecFCT2. While our old test system code has been a loyal companion since 2005 and been through a lot of maintenance and modifications, it was time to develop a new system that is designed in a modular way with an updated user interface. The goal has been to develop a production test system that has a much more modular design while keeping the functionality of the old production test system software.
To summon up, Hectronic has developed its own in-house general production testing software for more than two decades. Some installations that were installed 15 years ago are still up and running and in use today. It is essential that the production test equipment is regarded as a longtime commitment in regards to manufacturing embedded systems, they need to be maintained and supported for a long time after the installation. Any production test system needs to be able to live at least as long as the product they were designed to test. Otherwise, there will, sooner of later, be production issues.